How Factories Acid Wash Jeans: Chemicals & Techniques
What Do Factories Use to Acid-Wash Jeans?
Featured Snippet: Factories strip indigo pigment with oxidizers like sodium hypochlorite or potassium permanganate, often alongside pumice stones for abrasion. After bleaching, they neutralize with sodium bisulfite, rinse thoroughly, then finish with softeners. Modern plants may swap stones for enzyme or ozone treatments to save water and protect fibers, ensuring each jean emerges with consistent color and durability.
1. What chemicals do factories use to acid-wash jeans?
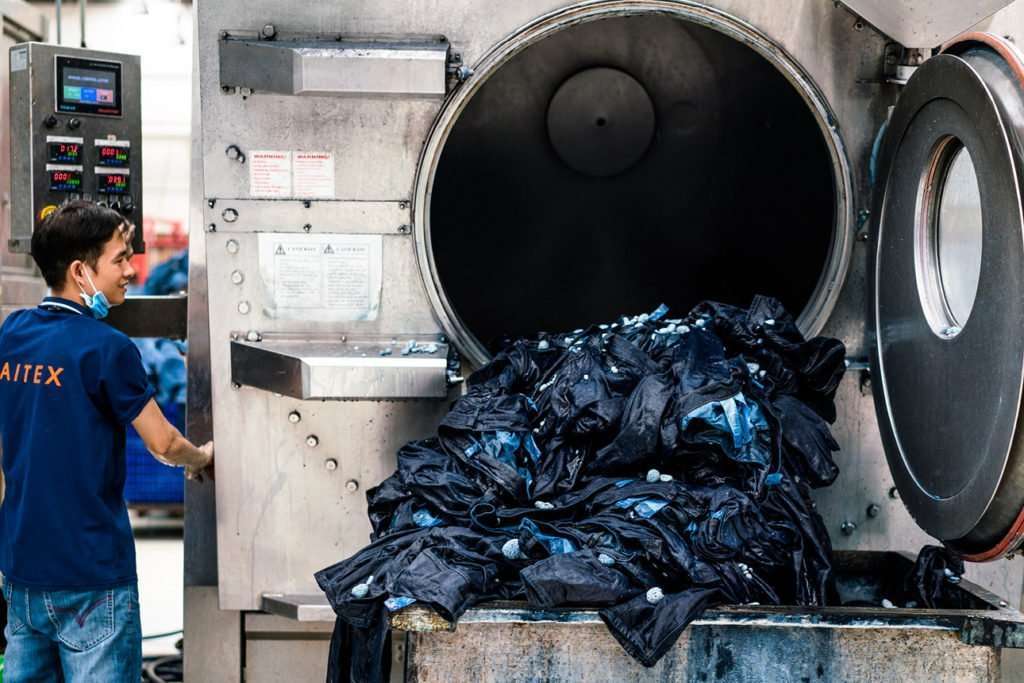
Snippet: The staple oxidizers are sodium hypochlorite (common bleach) or potassium permanganate, which break down indigo dye. Neutralizers like sodium bisulfite halt bleaching and restore pH. Eco-alternatives include cellulase enzymes and ozone gas, which deliver fading with less water and fiber damage.
Dive Deeper
1.1 Oxidizers vs. Neutralizers
·Sodium Hypochlorite: Fast-acting, cheap, strips pigment in 15–20 minutes.
·Potassium Permanganate: Creates bold contrast in 10–15 minutes but requires extra rinsing to avoid purple staining.
·Sodium Bisulfite: Neutralizes residual oxidizer, bringing fabric pH down to a safe 6–7.
1.2 Eco-Friendly Replacements
Treatment Type | Active Agent | Water Use Reduction | Fiber Strength Loss | Typical Cycle Time |
Bleach Wash | NaOCl | Baseline | 8–12% | 20 min |
Permanganate Wash | KMnO₄ | Baseline | 10–15% | 15 min |
Enzyme Wash | Cellulase | –35% | 3–5% | 45 min |
Ozone Treatment | O₃ gas | –70% | <2% | 30 min |
·Note: Data are averages from 2024 pilot studies across five factories.
1.3 Why It Matters
·Cost vs. Quality: Bleach is ultra-cheap ($2–3/kg) pay off in reduced fabric waste and wastewater fees.
·Environmental Impact: Switching to ozone can save 70% of water and eliminate chlorine discharge.
2. How do factories perform the acid-wash process to make acid-wash jeans?
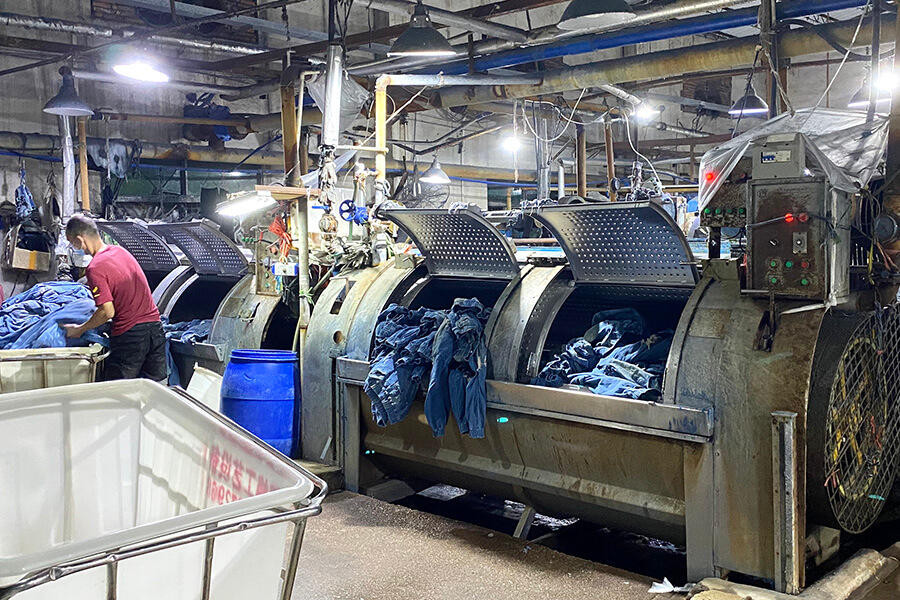
Snippet: Jeans tumble with pumice stones or beneath spray nozzles that douse them in oxidizer. After 20–30 minutes, garments are rinsed, neutralized, then given a final wash with softeners. Modern lines auto-adjust pH, temperature, and timing for repeatable results.
2.1 Step-by-Step Breakdown
·Prep & Loading (5 min): Jeans and stones (or spray racks) loaded into the drum.
·Oxidizer Stage (20–30 min): Automated dosing pumps deliver bleach or permanganate.
·Rapid Rinse (5–10 min): Immediate flush to stop over-bleaching.
·Neutralization Bath (10 min): Sodium bisulfite adjusts pH back to 6–7.
·Final Wash & Dry (15–20 min): Softeners added; jeans tumble dry at 60–70 °C.
Total Cycle: Approximately 60–75 minutes per batch.
2.2 Comparing Workflows
Workflow | Mechanical Action | Chemical Focus | Avg. Batch Size | Water per Batch |
Stone-Acid Wash | 1 kg pumice per 10 kg | 0.5 kg bleach | 200 kg | 1,200 L |
Spray-Acid Wash | No stones, spray bars | 0.4 kg bleach | 300 kg | 900 L |
Ozone-Only | No stones, ozone bath | Ozone generator | 150 kg | 350 L |
Enzyme Wash | No stones, enzyme tank | 0.2 kg cellulase | 100 kg | 800 L |
2.3 Critical Perspectives
·Throughput vs. Eco-Friendliness: Larger batches favor spray/bleach for speed; niche lines choose ozone or enzymes to market “sustainable denim.”
·Consistency Challenge: Pumice stones vary in shape and size, leading to batch-by-batch variation—automated sprays deliver more uniform fades.
3. Which tools and materials facilitate stone-washing versus acid-washing?
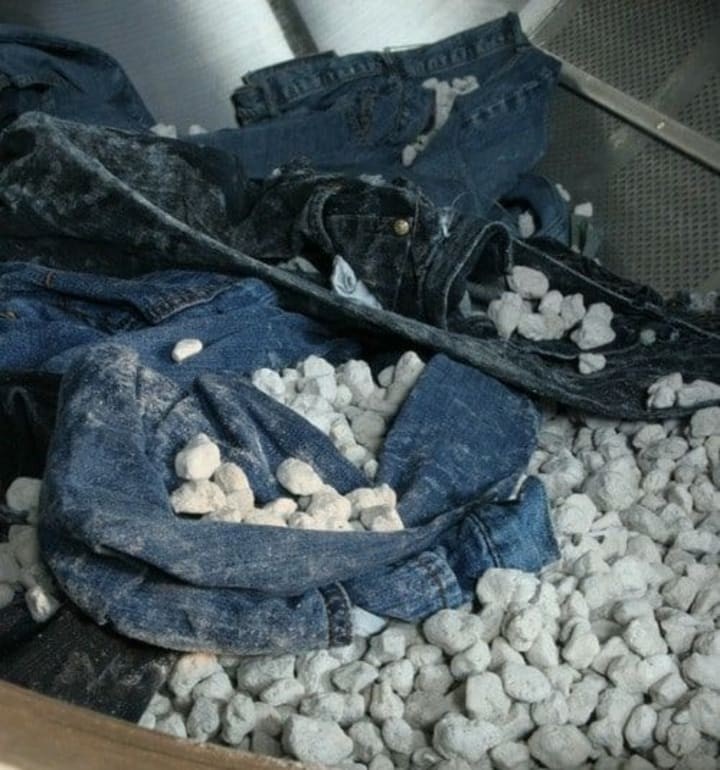
Snippet: Stone wash relies on natural or synthetic pumice; acid wash adds spray bars or dipping tanks for chemicals. Innovative plants use ozone chambers or enzyme dosing rigs to cut water use and keep fibers intact.
Dive Deeper
3.1 Pumice Stones: Old-School Abrasion
·Natural Pumice: Irregular shapes yield authentic vintage patterns but clog filters.
·Synthetic Beads: Reusable, uniform abrasion—higher upfront cost ($5/kg vs. $1/kg).
3.2 Spray & Injector Systems
·High-Pressure Nozzles: Coat jeans evenly, cut stone use by 60%.
·Automated Dosing: PLC-controlled pumps regulate chemical concentration, temperature, and pH.
3.3 Eco-Innovations
·Ozone Chambers: Jeans hang in sealed tubes; ozone gas bleaches in 30 minutes, zero liquid discharge.
·Enzyme Dosing Units: Precisely timed to deliver fade without over-weakening cotton.
3.4 What to Watch For
·Maintenance Needs: Spray nozzles block easily if water quality is low—regular back-flushing required.
·Worker Safety: Enclosed ozone chambers and closed-loop chemical dosing reduce operator exposure to fumes and dust.
4. How do stone-washed jeans vs. acid-washed jeans compare in look, feel, and durability?
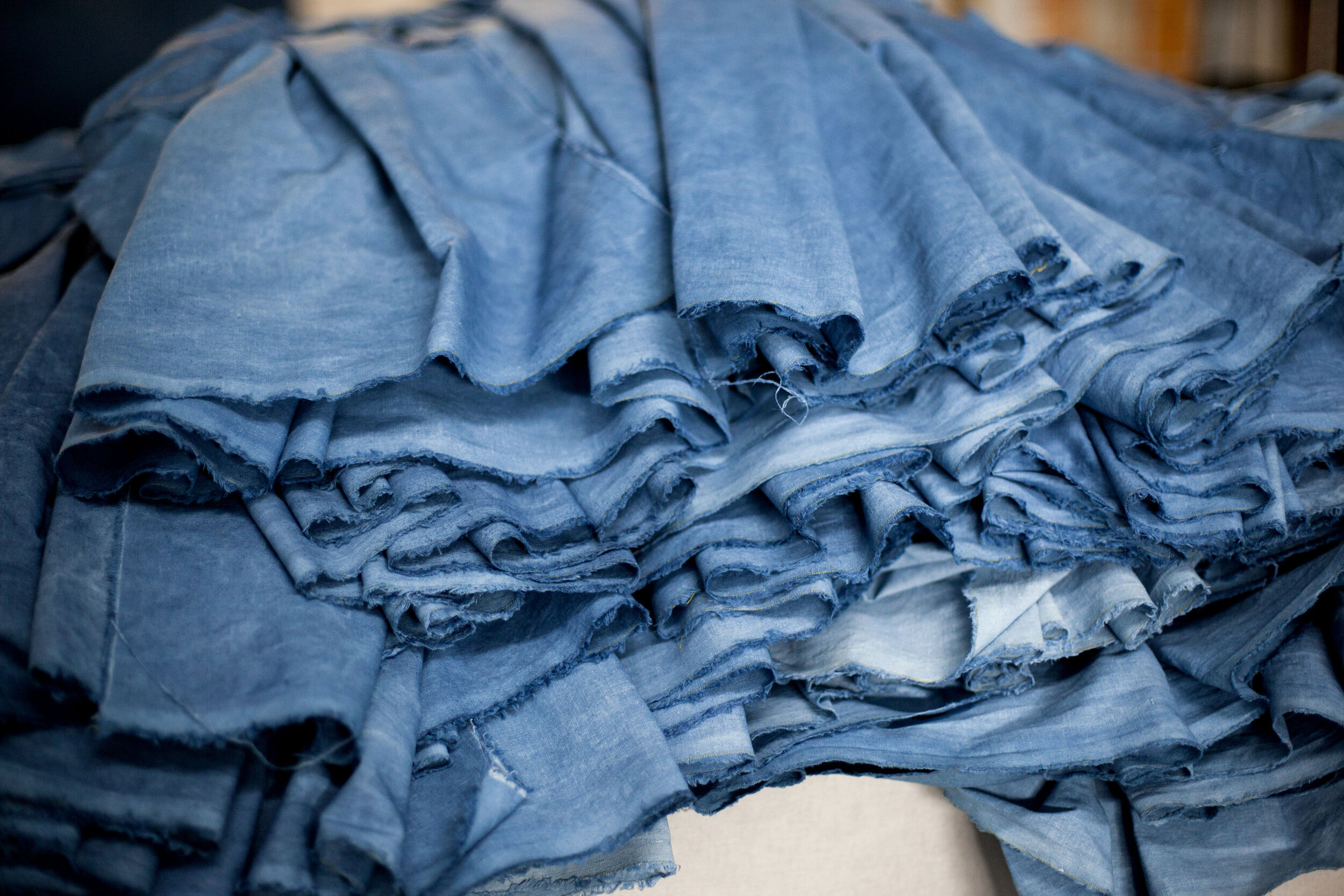
Snippet: Stone-washed jeans feel softer with gentle gradient fades. Acid-washed jeans boast stark, edgy contrast but may lose 8–12% of tensile strength. Enzyme and ozone treatments strike a middle ground—subtle fades with minimal fiber damage.
Dive Deeper
4.1 Side-by-Side Comparison
Attribute | Stone-Wash | Acid-Wash | Enzyme/Ozone |
Fade Appearance | Soft, gradual | Sharp, high-contrast | Controlled, uniform |
Hand Feel | Soft, broken-in | Slightly crisp | Soft with slight texture |
Fiber Strength ↓ | ~5% | ~10% | ~2–4% |
Environmental Hit | Medium (sediment) | High (chlorine waste) | Low (biodegradable/none) |
4.2 Consumer Trends
·Streetwear A-listers: Snap up acid-wash for that photographic pop.
·Eco-Conscious Shoppers: Seek enzyme or ozone washes, often paying 10–20% premium.
4.3 Durability & Care Tips
·Stone-Wash: Machine wash cold, gentle cycle; avoid bleach to maintain soft texture.
·Acid-Wash: Turn inside out; low-spin dryer or air-dry to prevent over-fading.
·Enzyme/Ozone: Standard denim care applies; less risk of over-bleach.
4.4 Critical Lens
·Is the extra “pop” worth the shorter lifespan?
·How do care instructions influence warranty claims and returns?
5. What impact did the acid-wash jeans movement have on denim fashion history?
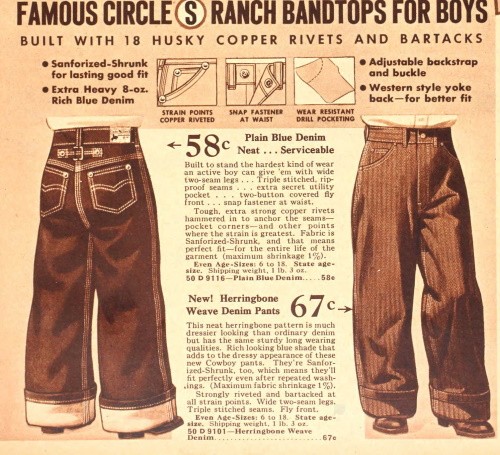
Snippet: Born in the early ’80s punk scene, acid-washed denim exploded by 1986 when 30% of U.S. denim sales featured bleach-faded styles. The trend resurfaces every decade—from Timberlake’s 2000s videos to TikTok’s #AcidWashChallenge in 2024—proving its lasting cultural pull.
5.1 Punk Roots & Mainstream Boom
·1980–1983: DIY punks bleached their pairs for a rebellious aesthetic.
·1984–1986: Levi’s and Wrangler launch factory-made acid-wash lines; sales spike 200%.
5.2 Revival Waves
Era | Catalyst | Notable Moment |
2000s | Celebrity endorsements | JT’s “Cry Me a River” music video |
2010s | Vintage thrift resurgence | Street style blogs, fashion weeks |
2020s | Social media challenges | #AcidWashChallenge on TikTok (2024) |
5.3 Modern Takes
·Acid-Wash Jeans Mens: Tailored slim cuts with strategic high-contrast panels.
·Event-Ready Denim: One-off factory washes for concerts, festivals, and influencer promos.
5.4 Critical Reflection
·Does nostalgia alone fuel revivals, or have new techniques improved the product?
·How does eco-awareness shape what “retro” really means today?
6. Are there eco-friendly or small-batch alternatives to large-scale acid-washing?
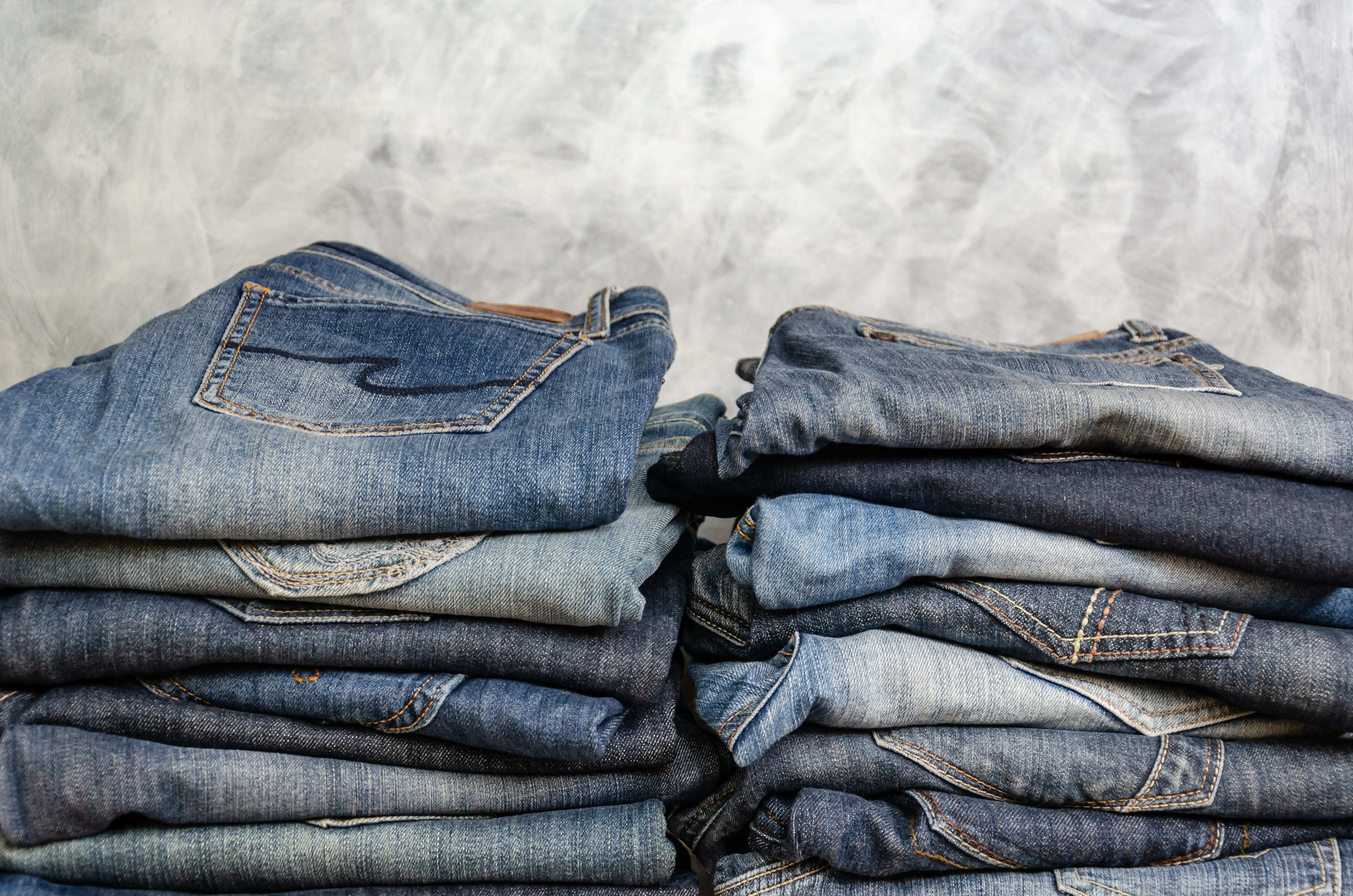
Snippet: Yes! Enzyme washes cut water by ~40%, ozone by ~70%, and lasers can burn fade lines sans chemicals. DiZNEW’s small-batch studios handle MOQs as low as 30 pieces, turning around custom washes in 2–3 weeks with high sustainability ratings.
Dive Deeper
6.1 Green Washing Technologies
Technology | Water Savings | Chemical Discharge | Avg. Cost/kg | Batch MOQ | Lead Time |
Enzyme Wash | –35% | Biodegradable | $2.50 | 50 pcs | 3 weeks |
Ozone Wash | –70% | Zero residue | $3.00 | 30 pcs | 2 weeks |
Laser Fading | –100% | None | $4.50 | 100 pcs | 4 weeks |
6.2 “Near Me” Custom
·Small-Batch Plants: Accept 30–100 pcs; service local designers and limited editions.
·Pop-Up Wash Studios: Mobile ozone units for on-site denim events and workshops.
6.3 Critical Takeaways
·Are consumers willing to pay a ~20–30% premium for greener washes?
·Can these techs scale for large global brands, or remain boutique-only?
7. Which safety, quality-control, and wastewater-treatment measures do factories implement?
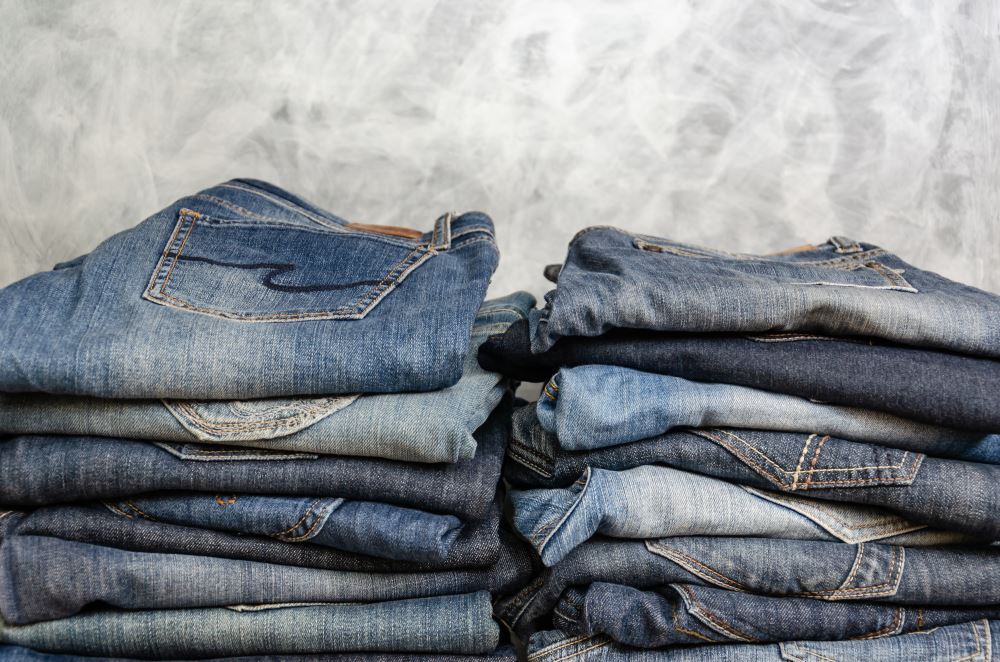
Snippet: Industrial plants neutralize bleach baths, filter out stone sediment, then run effluent through primary (sedimentation), secondary (biological), and tertiary (activated carbon/membrane) treatment. Inline sensors track pH, color consistency, and tensile strength to ensure every jean meets spec.
Dive Deeper
7.1 Effluent Treatment Stages
Stage | Purpose | Typical Removal Rates |
Primary | Sediment & grease separation | 50–60% solids removal |
Secondary | Biological breakdown of organics | 80–90% BOD/COD removal |
Tertiary | Micro-pollutant & color removal | 95–99% targeted removal |
7.2 In-Process QC Checks
·Colorimeter: Confirms ΔE < 2 across samples.
·Tensile Tester: Rejects batches losing >12% strength.
·Visual & Hand-Feel: Spot-checks for streak uniformity and softness.
7.3 Worker & Environmental Safety
·Closed-loop chemical dosing minimizes operator contact.
·Dust collectors and fume hoods capture pumice and bleach vapors.
·ETP sludge is de-watered and disposed per local regulations.
7.4 Critical Lens
·Are facilities keeping pace with tightening discharge limits (e.g., EU’s Zero Discharge of Hazardous Chemicals by 2025)?
·How do transparent sustainability reports build brand trust in the denim community?
1.How are acid washed jeans made?
Acid-washed jeans are created by treating denim with chlorine bleach and pumice stones or rubber balls in industrial washing machines, triggering a chemical reaction that selectively removes indigo dye to produce distinctive marbled patterns, while modern eco-conscious methods now utilize ozone gas or laser technology to achieve similar effects with reduced environmental impact.
2.What chemicals are used to dye jeans?
Traditional denim dyeing primarily uses indigo (synthetic or natural) and sulfur-based compounds to achieve classic blue/black hues, while modern sustainable methods employ eco-friendly synthetic vat dyes, reduced-chemical foam applications, and emerging plant-based alternatives like natural indigofera or waste-derived pigments, with brands increasingly adopting GOTS-certified processes and Leather Working Group standards to minimize environmental impact.
3.What is used to bleach jeans?
Jeans bleaching traditionally employs chlorine bleach or sodium hypochlorite for color stripping, while eco-conscious manufacturers now utilize hydrogen peroxide, ozone gas, and laser finishing combined with enzyme wash techniques to achieve distressed looks with reduced water consumption and chemical residues, meeting OEKO-TEX® standards for safer textile production.
4.How do they stone wash jeans?
Stone washing jeans involves tumbling denim with pumice stones and chlorine bleach in industrial machines to create abrasions, while modern sustainable methods replace stones with enzyme washes, rubber pellets, or laser distressing to achieve vintage looks using 50% less water and energy, aligning with eco-friendly denim trends and ISO 14001-certified production standards.
Conclusion
From testing bleach concentrations to choosing between stones or laser beams, modern acid-wash production is as much science as it is art. At DiZNEW, we marry advanced tech with strict quality and environmental standards—offering bespoke OEM/ODM runs starting at just 30 pieces. Whether you crave that high-contrast ’80s pop or a gentle, eco-friendly fade, our team is ready to craft your next standout denim collection.
Ready for your own custom acid-washed jeans? Contact DiZNEW today to discuss your design, materials, and sustainable wash preferences—let’s bring your denim vision to life!