Denim Jeans Materials: Key Components & Fabric
What are the raw materials required for making denim jeans?
Snippet: Denim jeans require primarily long-staple ring-spun cotton yarn, indigo or sulfur dyes, and metal hardware (rivets, buttons, zippers), plus elastane (1–3%) for stretch, pocketing fabrics, and specialized threads—finished via washing, enzyme, or laser processes to achieve that signature hand feel and look.
1.What is denim, and what makes blue jeans unique?
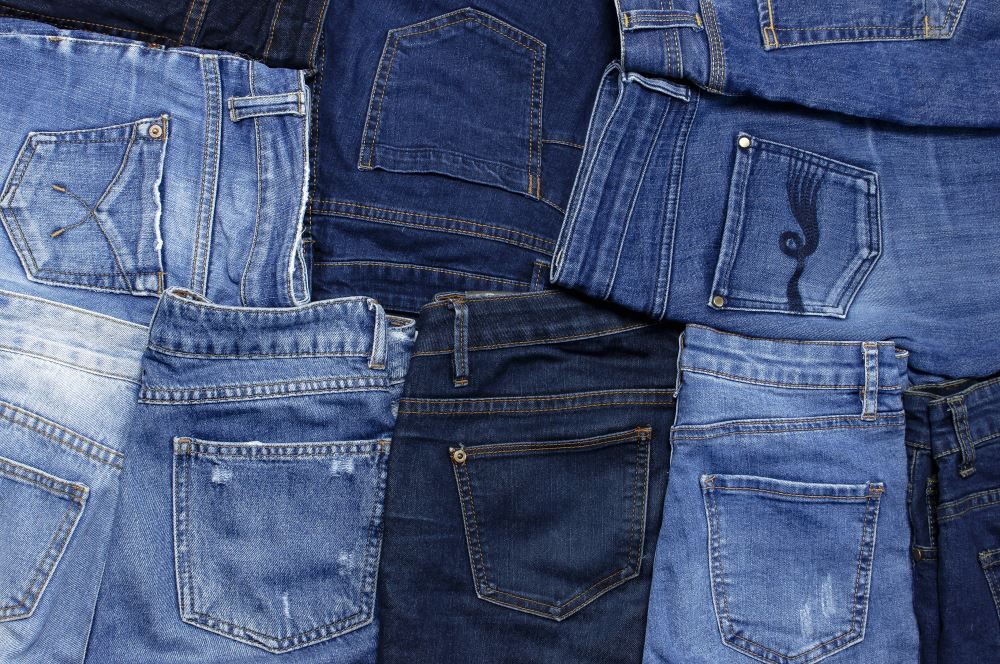
Snippet: Denim is a sturdy twill-woven cotton fabric; blue jeans get their signature hue from repeatedly dipping the warp yarns in indigo dye—creating a surface color that fades with wear, yielding unique patterns and a lived-in look.
Dive Deeper
1.Origins and Weave
·Twill vs. Plain Weave: Twill’s diagonal ribs (2:1 or 3:1) give denim its strength. Lower weft count means more durability.
·Historical Snapshot: Started in 17th-century France (“serge de Nîmes”), popularized in USA by Levi Strauss (1873).
2.Indigo Dye Chemistry
·Vat Dyeing Steps:
①Reduction: Indigo powder → soluble leuco form in alkaline bath.
②Dipping: Yarns dipped 5–15 times—each dip adds ~5–7% depth.
③Oxidation: Yarns exposed to air to fix color.
·Fade Mechanics: Indigo sits on the surface; abrasion gradually removes dye, creating “whiskers” (front-thigh creases) and “honeycombs” (back-knee patterns).
3.Cultural Impact
·Worn by miners → cowboys → rock stars → streetwear icons.
·Today’s raw, selvedge, and distressed styles all trace back to indigo’s magic.
2.What essential raw materials are required for making denim jeans?
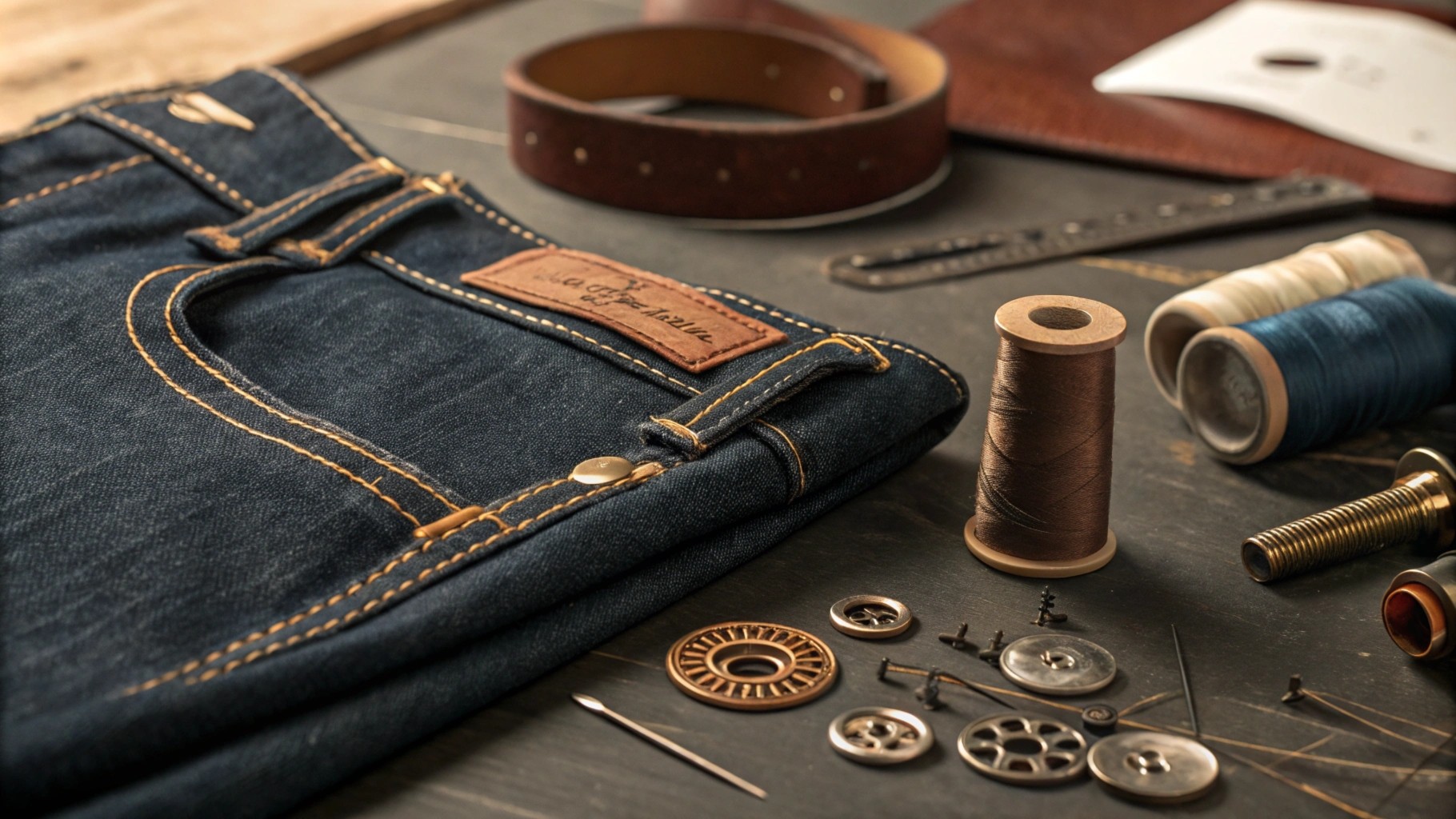
Snippet: Core ingredients include long-staple ring-spun cotton yarn, indigo or sulfur dyes, elastane (1–3%), metal hardware (rivets, zippers, buttons), pocket lining fabric, and high-strength threads—plus finishing chemicals like softeners and enzymes.
Dive Deeper
1.Core Material Breakdown
Material | Typical Specs | Purpose |
Cotton Yarn | Ring-spun; 30–14s Ne; 1.2–1.6 oz/yd² | Base fabric; strength & hand feel |
Indigo Dye | 1–5% owf*; 5–15 dips | Signature blue color |
Sulfur Dye | 1–3% owf | Blacks, greys, browns |
Elastane | 1–3% of fabric weight | Stretch & recovery |
Hardware | Rivets (copper/brass); metal zippers; jeans buttons | Reinforce stress points & closures |
Pocketing Fabric | 100% cotton or cotton/poly blend | Reduce bulk inside pockets |
Thread | Polyester core-spun; 40–100 wt | Seam strength; color matching |
Chemicals | Softeners, levelling agents, fixatives | Aid dye uptake & hand fee |
2.Why Long-Staple Cotton?
·Fiber Length: 32–35 mm yields smoother, stronger yarns.
·Tensile Strength: +15% stronger than short-staple cotton.
3.Hardware Choices
·Rivets: Typical pull-strength ≥ 150 N.
·Zippers: YKK #5 metal zippers are industry standard.
·Buttons: Die-cast brass or stainless steel for corrosion resistance.
3.How is raw denim produced, and what goes into making raw denim jeans?
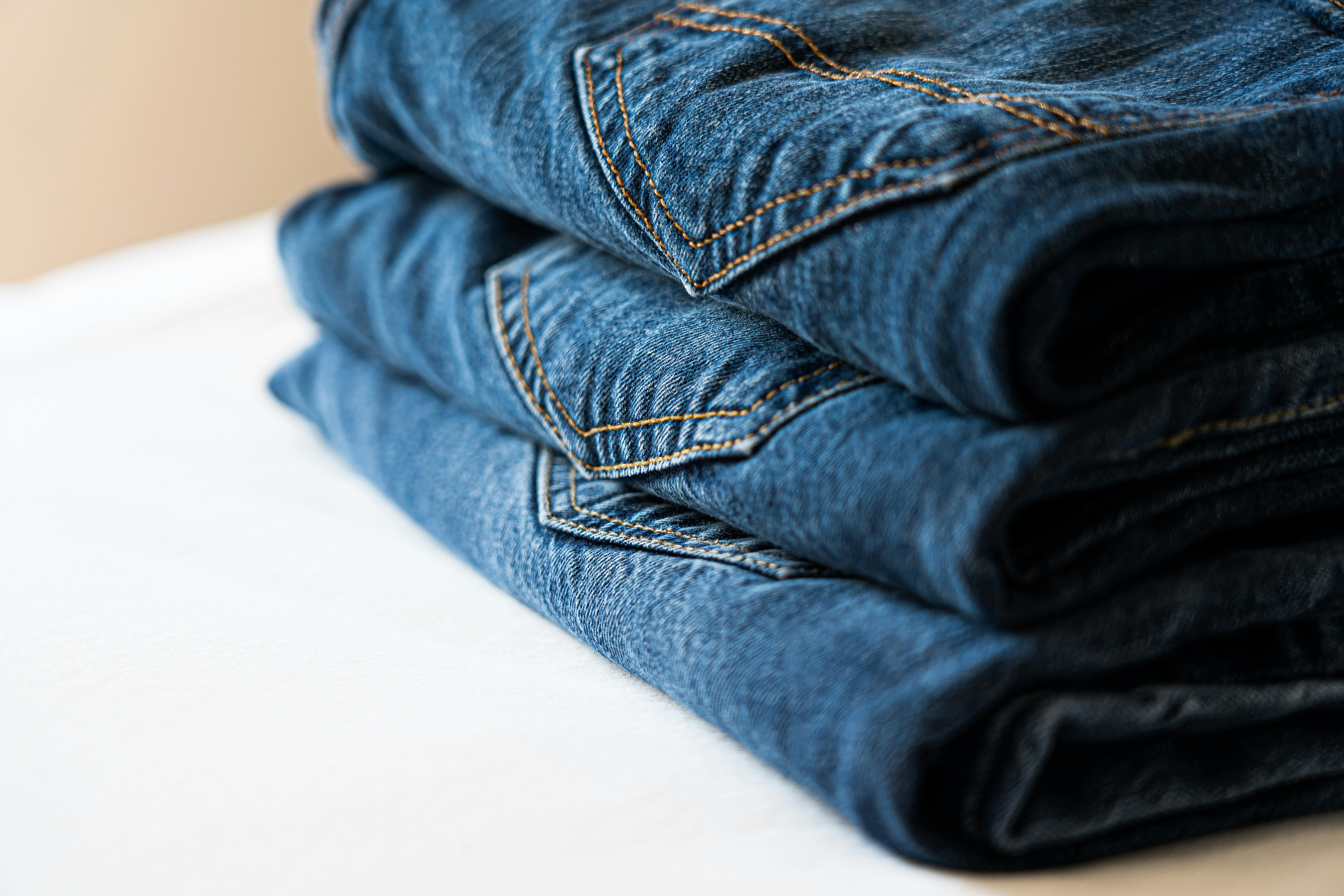
Snippet: Raw denim is woven from indigo-dyed warp and natural weft yarns, then cut and sewn without pre-wash or distressing—preserving starch and sizing for a stiff hand and personalized fade over time.
Dive Deeper
1.Fabric Production
·Warp Sizing: Starch or PVA sizing boosts yarn strength by 30–50% for weaving.
·Weaving: Projectile or rapier looms produce 12–14 oz/yd² fabric with minimal defects.
2.Cutting & Assembly
·Pattern Efficiency: CAD nesting achieves up to 97% fabric utilization.
·Chain-Stitching: Creates the classic “rolled” hem and a distinct chain-stitch ID on the back
3.No-Wash Benefits & Caveats
·Benefits:
·Personalized wear patterns.
·Less water/chemical use up-front.
·Caveats:
·Initial stiffness can feel uncomfortable.
·Up to 5% shrinkage if not sanforized.
4.Critical Perspective
·Raw denim’s eco-benefits depend on end-user wash frequency. If someone machine-washes raw denim weekly, water savings vanish.
4.How are jeans made step-by-step?
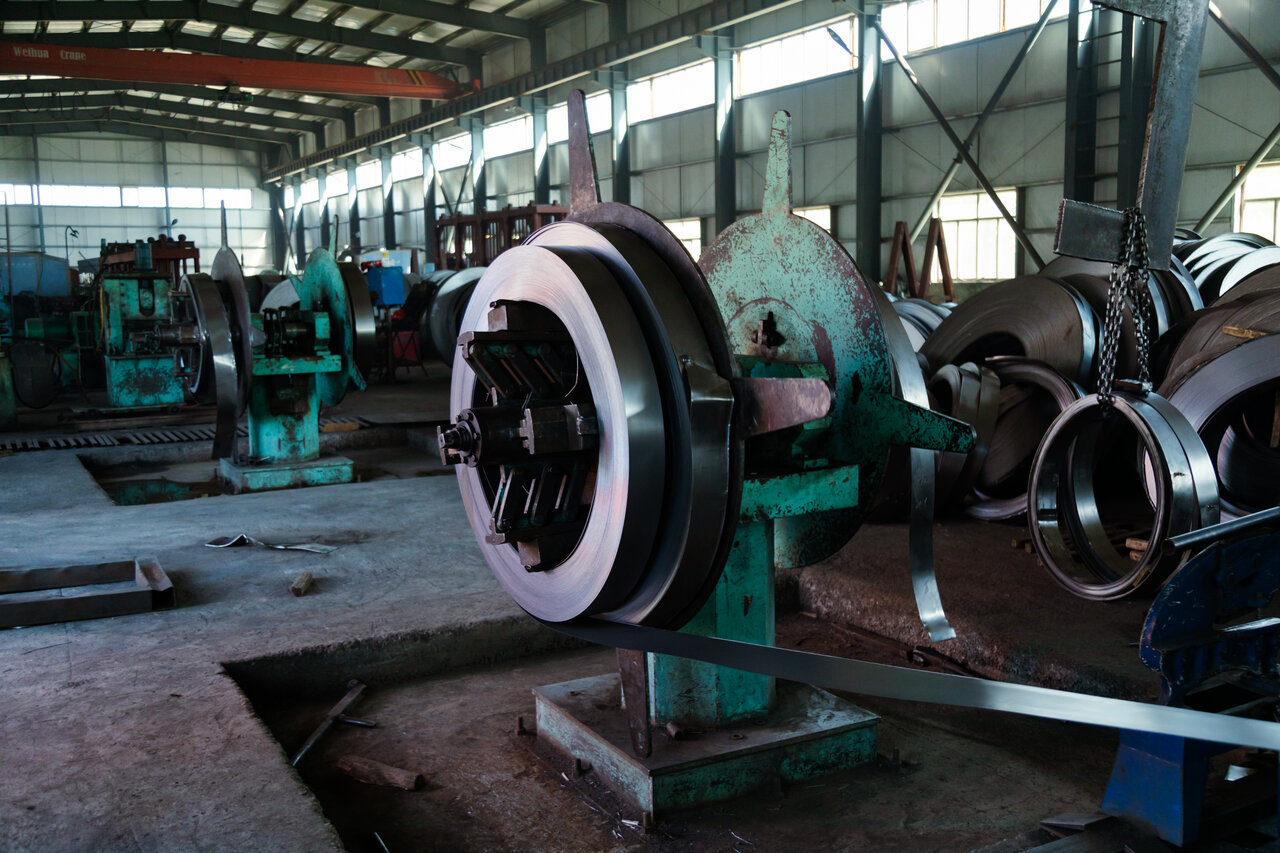
Snippet: Design → pattern making → fabric cutting → sewing panels → hardware installation → finishing (washing, distressing, coating) → quality control → packaging—each step balancing efficiency and craftsmanship.
1.Design & Tech Pack
·3D CAD models shorten fit iterations by ~30%.
2.Pattern Making
·Digital patterns plus marker planning reduce fabric waste by up to 15%.
3.Cutting
·Laser vs. die: laser gives ±0.5 mm precision.
4.Sewing & Assembly
·Overlock seams, double-stitch chain-seams, bartacks at 7 stitches/cm.
5.Hardware
·Automated pressing for buttons/rivets; manual checks ensure alignment.
6.Finishing
·Average wash cycle uses 20–80 L water; ozone/laser reduce that dramatically.
7.QC & Packaging
·100% visual inspection; random tensile tests to 150 N; packed in recycled cartons.
5.How are jeans manufactured with water-saving processes?

Snippet: Modern techniques like ozone washing (5–10 L/pair), foam dyeing (<5 L/kg), and laser abrasion slash water usage up to 90% compared to traditional stone washing (50–80 L/pair).
Process | Water Use per Pair | Key Benefit |
Stone Wash | 50–80 L | Soft hand, vintage look |
Enzyme Wash | 20–30 L | Softer hand, less mechanical damage |
Ozone Wash | 5–10 L | Fewer chemicals; whiteness control |
Foam Dyeing | <5 L/kg | Uniform dye; minimal effluent |
Laser Distress | 0 L | Precise patterns; no water |
Beyond Water
·Effluent Treatment: Modern plants recycle ≥ 70% of process water.
·Energy Footprint: Ozone and laser require higher electricity but offset by water/chemical savings.
·Circularity: Denim scraps can be re-spun; mixed-fiber blends make recycling harder.
6.Is denim cotton or polyester, and which auxiliary fibers are added?
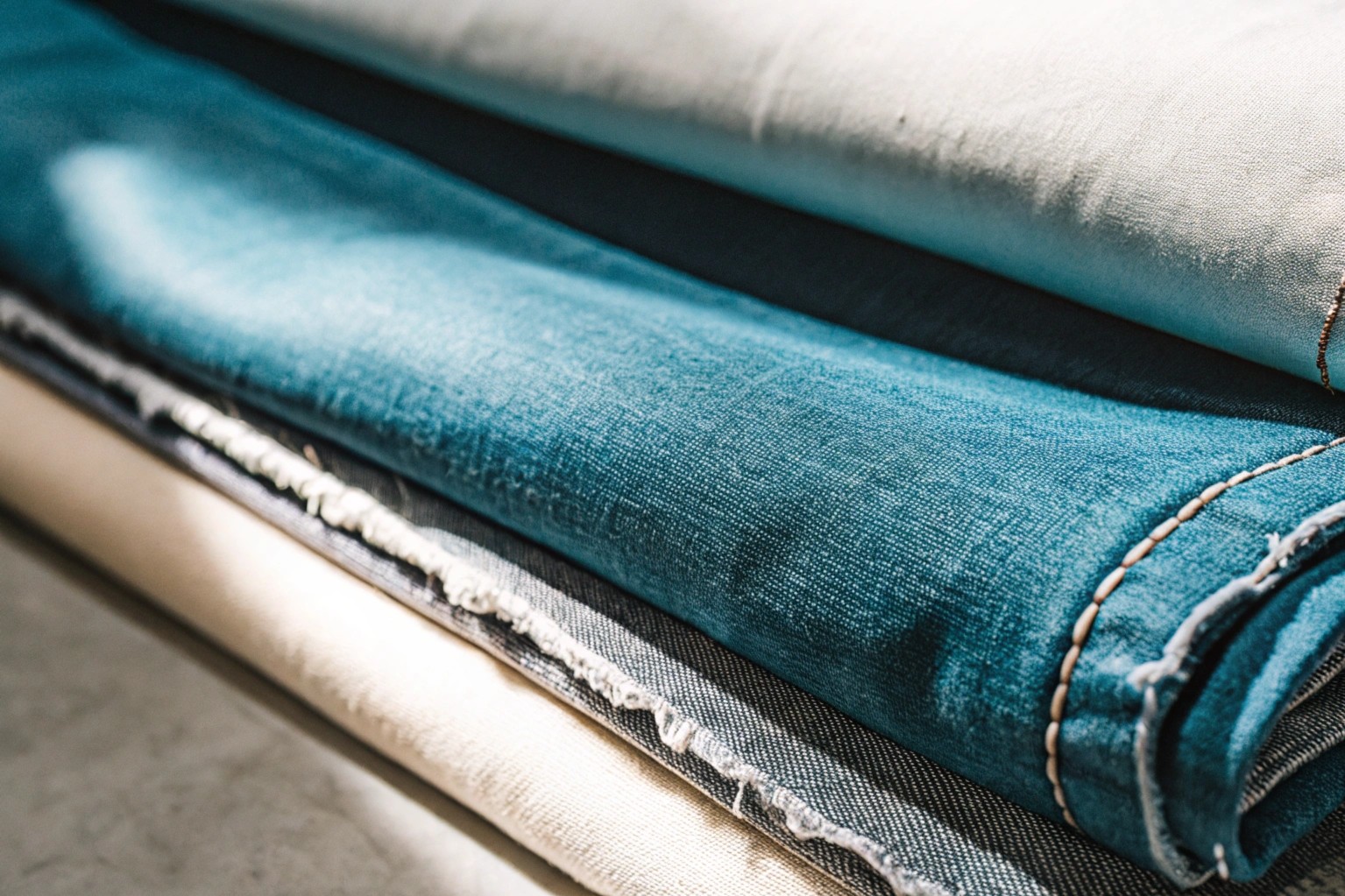
Snippet: Denim is mainly 100% cotton, but 1–3% elastane (for stretch) or up to 30% polyester (for durability) are common—each blend chosen based on target use (skinny fit vs. workwear).
Dive Deeper
Blend Type | Composition | Key Properties |
100% Cotton | 100% cotton | Natural hand feel; vertical shrinkage |
Cotton–Elastane | 97–99% cotton + 1–3% elastane | Stretch & recovery; snug fit |
Cotton–Polyester | 70–80% cotton + 20–30% polyester | Durability; wrinkle resistance |
Cotton–Lyocell | 60–70% cotton + 30–40% lyocell | Moisture wicking; softer hand |
1.Fit & Function
·Skinny & Jeggings: Elastane blends for up to 50% stretch.
·Workwear & Utility: Polyester for abrasion resistance, quick dry.
2.Sustainability Trade-Offs
·Synthetic Fibers: Derived from petrochemicals; may shed microplastics.
·Recycling Complexity: Blended fabrics often down-cycled rather than fully recycled.
1.What are the raw materials for denim jeans?
The primary raw materials for denim jeans are cotton yarn (indigo-dyed warp and undyed weft), with modern blends often incorporating elastane/spandex for stretch, polyester for durability, and sustainable alternatives like organic cotton, hemp, or recycled fibers to reduce environmental impact.
2.What are denim jeans made of?
Denim jeans are traditionally made from tightly woven cotton twill fabric, dyed with indigo for the classic blue hue, but modern variations include elastane for stretch, recycled polyester for durability, and sustainable options like organic cotton, hemp, or Tencel™, while premium styles may feature selvedge denim or eco-friendly dyeing techniques.
3.What is raw denim made of?
Raw denim is crafted from 100% cotton, typically using unwashed, unsanforized yarns dyed with natural indigo or sulfur for depth, with premium selvedge denim featuring tightly woven ring-spun threads on vintage shuttle looms, while eco-focused versions may blend hemp or use plant-based dyes for artisanal authenticity and reduced water waste.
4.What are the ingredients in denim?
Denim's core ingredients are cotton fibers, indigo dye (for the classic blue hue), and sulfur dyes (for black/gray shades), with modern variations adding synthetic additives like elastane for stretch or sustainable materials like recycled polyester, organic cotton, or lyocell, while traditional twill weaving and eco-innovations like waterless dyeing or biodegradable finishes refine its texture and environmental footprint.
Conlusion
From cotton fields to finished stitches, the journey of denim raw materials is complex—but armed with real data, tables, and a critical eye, you can choose the exact specs that fit your brand’s story and performance needs. At DiZNEW, we leverage advanced equipment, strict QC, and low-MOQ flexibility (30 pieces) to deliver tailored OEM/ODM solutions for streetwear, workwear, festivals, and beyond.
Ready to bring your custom denim vision to life? Contact DiZNEW today for a no-obligation quote and let’s craft your next signature pair—sustainably, precisely, and with that unmistakable DiZNEW touch.